Quality Process: Our Quality Control is put into action as soon as the material for manufacturing of components
comes through the door. The material is inspected to assure that it conforms to the specifications. Upon approval it is
put into use. We require material certs from the vendor that are kept on file so that we may have full traceability at all
times. Any rejected material is appropriately tagged and returned to the vendor. Once a job is started on a machine, a sample
of the component is made for inspection. The sample is kept as a first article providing it meets all criteria of the print
supplied. First Articles are kept at our facility at all times in order for traceability. Once a job is put into full production,
spot inspections occur throughout the day and throughout the entire phase of the job. Each day the components are collected
to be put through a cleaning process. Each days work is inspected for cleanliness. If the components are not passed for
cleanliness they are put through the cleaning process again. Another inspection of the components is made to assure they
conform to the print. If any deviations are found the components are appropriately tagged and sent to be reworked or scrapped.
If the components pass all criteria, they are stored in a container ready for final inspection. Once a job is completed,
a final inspection is performed on the entire batch of components. Upon passing, the components are shipped to the customer.
If the components fail they are sent to be reworked or scrapped.
|
 |
 |
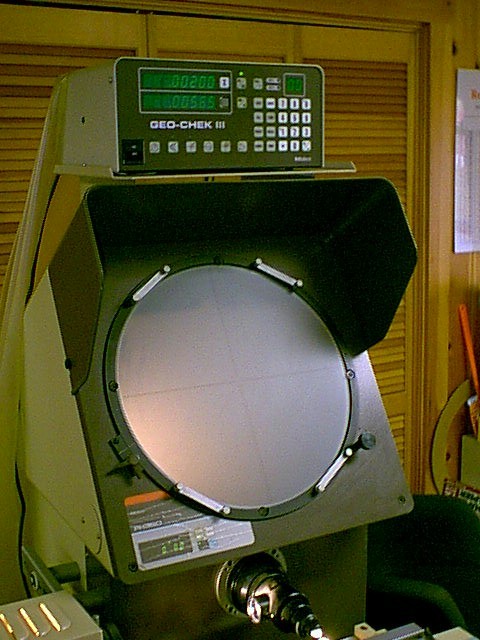
Mitutoyo Profile Projector PH350
|
 |
 |
Inspection and Measuring Devices: * Mitutoyo Profile Projector PH350 * Setra 5000C Electronic Scale
* Mitutoyo Geo-Check III Digital Read-Out * Mitutoyo Digital Micrometers * Blade Micrometers
* Nikon 35 Power Microscope * Meiji Techno 45 Power Microscope
|
 |
|
 |
|